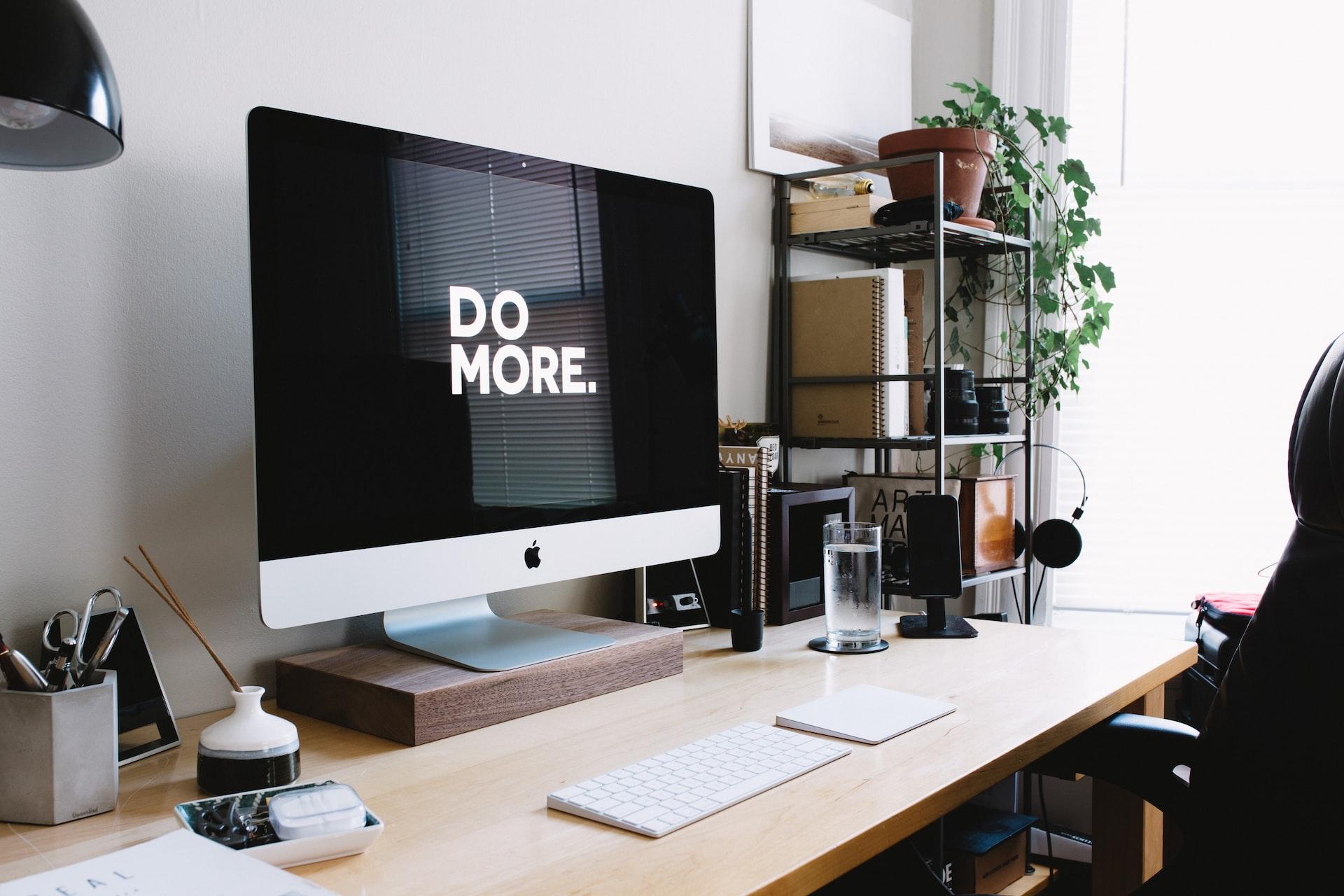
Process Automation
Put your business processes on Steroids
and do more in less time.
What is Process Automation?
Process automation uses technology to automate complex business processes. It typically has three functions: automating processes, centralizing information, and reducing the requirement for input from people. It is designed to remove bottlenecks, reduce errors and loss of data, all while increasing transparency, communication across departments, and speed of processing.
Think about a car wash. The process, which is fully automated, looks something like this:
- The customer chooses which wash type they want
- System requests payment from the customer
- Takes payment from the customer
- Approves transaction and advises customer to drive into the carwash
- Identifies when the car is in the right position using a sensor and advises the driver to stop
- Uses a range of sensors to identify the car’s height and size
- Runs the pre-selected and paid program. This includes a number of variables, including rinsing, washing with soap and brushes, wax application and blow-drying the car
- When complete, advises the customer to exit the carwash.
While a very simple automation, this process is one that most people are familiar with, and seamlessly integrates a digital transaction and input from the customer and turns it into a mechanical series of automations using software, hardware, and communication to an accounting system.
Process automation streamlines a system by removing human inputs, which decreases errors, increases speed of delivery, boosts quality, minimizes costs, and simplifies the business process. It incorporates software tools, people, and processes to create a completely automated workflow.
Process Automation vs Robotic Process Automation
Some people use these two terms interchangeably. However, there are some important factors and differences between robotic process automation (RPA) and process automation. While they both automate business processes, that is where the similarities end.
Traditional process automation is much broader in its applications and integrations. It includes the use of machinery to perform tasks, software, data and storage systems, and integration activities. However, robotic process automation is focused on front-end activities, and emulates work in much the same way a human would.
Process automation often requires a large input from IT engineers and developers, while robotic process automation uses robots that can be trained or are self-trained. RPA is generally used for IT functions like email replies, data extraction, and other basic system tasks that a human would otherwise perform.
Business process automation covers a huge range of tasks, including:
- Managing and gathering data files
- Automating repetitive tasks
- Connecting and integrating data sources and services
When Would an Organization Use Process Automation?
Common processes to be automated include invoicing, sales orders, accounting reconciliation, data entry, system queries, payroll, employee or vendor on-boarding, or staff terminations.
A typical example of when process automation could be hugely beneficial is in a service company. They might start looking for a current process which has bottlenecks, is prone to errors, or has gaps in the system. For instance, a refrigeration service company wanting to automate their service sheet process could look like this:
- Call comes in from the customer over the phone. Details are taken down and a job manually created in a work system.
- The job is taken up by an engineer returning to base and picking up a physical piece of paper with the details on it.
- The engineer attends the job and writes on the job sheet the parts they used, the time taken, the distance travelled, and any other relevant information.
- The engineer goes home for the day. The following day, they return to the office and drop off their paperwork.
- The admin team manually processes the paperwork, updates the system, orders parts as required, and charges mileage and consumables.
- If the job is finished, the instance is closed on the invoicing system and the invoice sent out to the customer. If parts are on order or the job requires substantial labour, this cycle can continue indefinitely.
In that system, there are multiple places in the process where information can be lost, deadlines missed, paperwork left on site, or any number of other problems. Process automation takes away all of the opportunity for variance and problems.
Incorporation of hardware like smart phones give the ability for engineers to enter and receive data electronically. Using fleet monitoring systems, actual mileage can be taken from the daily use and automatically applied to the job.
Software plays a huge role in this. For instance, the engineer entering what parts they used may trigger an automatic alert to order more sensors or a type of cable or can even send an alert directly to the supplier. There is no need for manual approval of purchase orders, as the process is fully automated and generated by the system.Then once the work is complete, the information is already in the system, saving data entry and errors in the office.
These process automations can happen in any industry, and in any task that has multiple steps. Think of processes within a business that are repetitive and are prone to delays, such as loan processing and approvals, customer service, and approval management
How to Implement Process Automation
Every organization is different, but the five basic steps remain the same.
1. Identify Tasks and Process That Can Be Automated
Not every task can be automated. There are some easy wins though, where some processes can easily be automated with existing software. Think about tasks within an organization that:
- Are repetitive
- Are time sensitive
- Include a number of people and pieces
- Need auditing or compliance trails
- Impact other processes and systems within the business
- Are rule based, standardized
- Have the potential for high return on investment
Find these tasks and create a process map that shows the current system.
2. Set Your Organizational Goals
Unless you have a firm idea of where you want to go, your changes may not result in any positive, lasting change. The organization needs to decide what their goals are, and how automation will help to achieve them. Also it’s important to plan how success will be measured: less customer complaints, a drop in turnaround time, an increase in profitability?
Once you have clarified your goals, decision making becomes a lot easier, as every choice simply becomes is this taking us closer to our goals, or further away?
3. Choose the Right Tools
This is where research is required to find the best solutions. This could benefit from involving professionals who have had experience in creating successful process automation systems. The ideal system is simple and easy to understand, with intuitive interfaces and great usability. It should be scalable, with flexibility for future growth and change within the organization. It should also integrate with existing software and tooling, be able to communicate with other programs, and have a system to deal with data.
4. Change Management
This is arguably the most important step in transitioning to the new automation. Getting the buy-in of staff and training employees in the use of the software helps to ensure it is used effectively and with a positive attitude.
Involving the team with the planning process, getting a feedback loop that is open to change from both sides, and ongoing education all help to transition smoothly to the new process.
5. Measure and Monitor
Your new process, and the tools used, are not intended to be static. As the business needs change, so should the system. Continually monitor key performance indicators, and if performance drops, assess the process and re-evaluate needs that are vital to system longevity.
Benefits of Process Automation
With such a bespoke, holistic solution, process automation should deliver a raft of positives for any organization that implements it correctly.
Transparency in Management
The day to day business operations can quickly become all that management notices; the overarching strategy and process can get lost in the minutiae of running the organization. Sitting down, going over process workflows, and implementing process automation allows owners to truly see and understand the business. Clearly defined systems allow for deeper insights into the business and possibility for greater improvements in the future.
Improve Productivity
Business process automation continues to be the key to improving productivity for organizations. RPA alone has helped to improve productivity in businesses by 86 percent. Removing bottlenecks, taking manual, time-consuming tasks away from people, and seamlessly integrating everything into one automated workflow increases productivity dramatically for companies.
Increase Compliance
Whether with internal policy and standards or external governing bodies and agencies, process automation systems increase compliance. As all processes automatically happen, there are no cutting corners, no missed steps, and no forgotten steps in a process. If a business has governance, risk, or compliance concerns, process automation should be a vital part of their day-to-day operations.
Reduce Costs
One of the most attractive benefits of process automation is a reduction in costs. Businesses have reported a reduction of costs of 59 percent, which allows businesses to create more income, reinvest in the business, or grow. Return on investment was reportedly achieved in less than 12 months.
This is due a range of factors:
- Increased processing speed
- Less bottlenecks and delays
- Less errors
- Freeing up time for staff to perform other tasks
Better Utilisation of Staff
While staff are busy with tedious, repetitive tasks, they are not being used to their full potential. By removing these tasks and allocating employees to more valuable and interesting parts of the business, they will be more satisfied, increasing positive business outcomes.
Less Errors
Errors can be disruptive and create problems within a business. While getting an order wrong or having an incorrect address are problems that can be resolved, it takes up valuable time. If those problems start to affect customers, it can negatively impact the entire business, contribute to churn, and create more work for staff in the long term. Automation means much less capacity for errors.